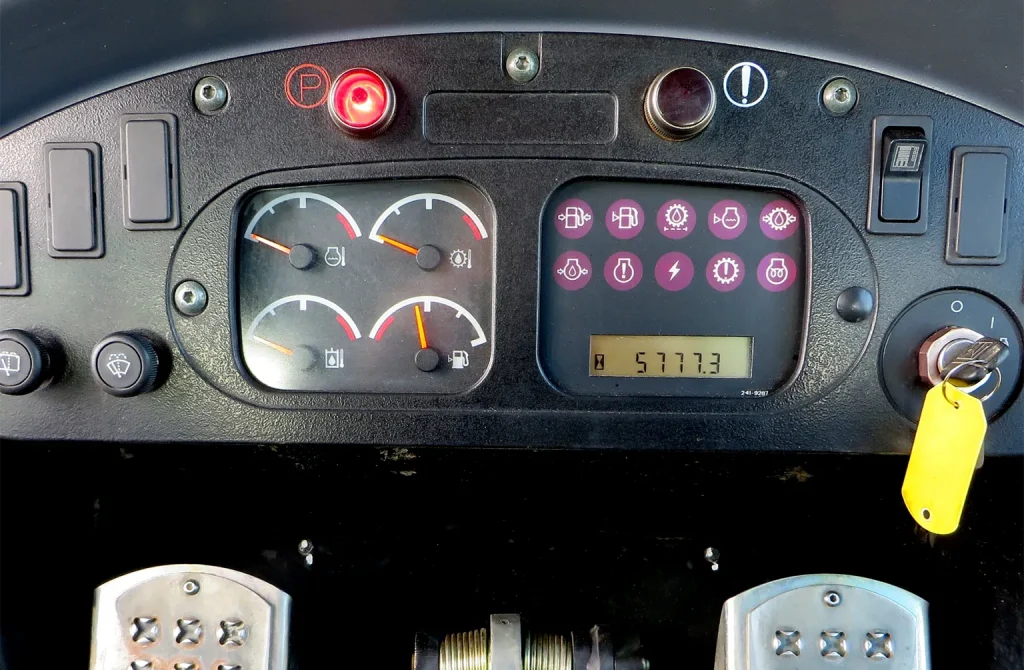
As global temperatures continue to rise, the construction industry faces new challenges in operating heavy machinery. High ambient temperatures can significantly impact both the machinery itself and the operators tasked with its use. It is essential to address these challenges proactively to ensure safety, minimize downtime, and extend the lifespan of equipment.
This newsletter provides practical tips and insights to help you maintain optimal performance in extreme heat. From technical checks to operator comfort, we cover everything you need to know to keep your operations running smoothly.
The Cooling System: Your First Line of Defense
One of the most critical systems in heavy machinery is the cooling system. Excessive heat can lead to lasting damage to key components if not properly managed. Here are steps to prepare your cooling system for operation in hot weather:
Pre-Operation Checklist
- Inspect Radiators, Hoses, and Coolant Levels: Ensure all components are in good condition and free of leaks.
- Clean Radiators and Fans: Dust and debris can clog these components, reducing cooling efficiency. Regular cleaning is crucial.
- Check Fan Belts: Look for signs of wear or slack that could compromise fan performance.
- Use Reversible Fans: Many modern machines are equipped with reversible fans that can expel accumulated dust by running in the opposite direction.
Is Pure Water a Good Coolant?
While tap water may seem like a convenient and inexpensive coolant, it’s far from ideal for heavy machinery. Here’s why:
Disadvantages of Tap Water
- Mineral Deposits: Depending on the region, tap water often contains dissolved minerals that can form limescale when heated. Limescale buildup reduces heat exchange efficiency and can lead to overheating.
- Lack of Corrosion Protection: Unlike modern coolants, tap water offers no protection against corrosion, leading to internal engine damage over time.
- Low Boiling Point: Water boils at 100°C (212°F), but modern coolants are engineered to withstand much higher temperatures, maintaining effective cooling even under extreme conditions.
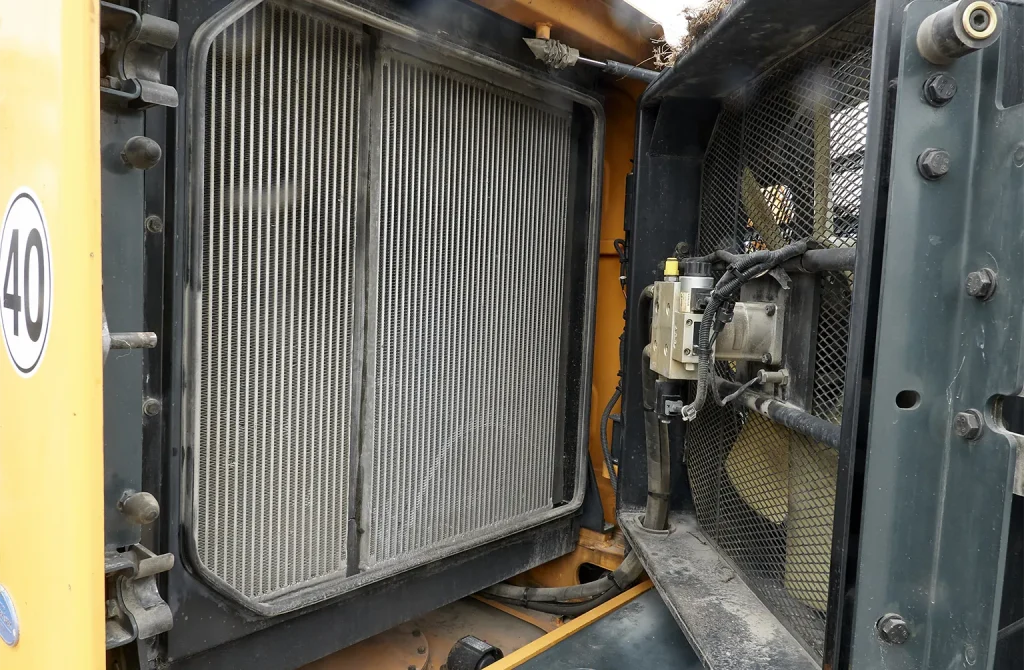
Modern Coolants
Modern coolants are specifically formulated to address these issues. They include corrosion inhibitors and have higher boiling points, ensuring consistent performance in demanding environments. Always use the coolant recommended by your equipment’s manufacturer.
Operational Best Practices in High Temperatures
Key Tips for Operators
- Monitor Temperature Gauges: Continuously check for signs of overheating and stop operation if necessary.
- Optimize Work Hours: Schedule heavy operations during cooler parts of the day, such as early morning or late evening.
- Avoid Overloading: Exceeding equipment capacity generates additional heat, placing unnecessary strain on the machinery.
- Clean After Use: Remove dust and debris from radiators, engines, and filters to ensure peak performance during the next use.
- Park Wisely: Whenever possible, park machinery in shaded or ventilated areas to reduce heat exposure during downtime.
When Cooling Capacity Isn’t Enough
Even with regular maintenance, extreme conditions can overwhelm standard cooling systems. Here are additional measures to consider:
Diagnostics and Adjustments
- Check Thermostats and Radiator Efficiency: Ensure thermostats are functioning properly and that the radiator is dissipating heat effectively.
- Inspect Hydraulic Systems: Verify that hydraulic oil is routed through the cooler. A clogged filter may trigger a bypass, sending hot fluid directly back into the tank.
Upgrades for Extreme Heat
- Install Additional Coolers: For regions with intense solar radiation or high operational demands (e.g., using hydraulic hammers), supplementary coolers can make a significant difference.
- Use High-Temperature Conversion Kits: Many manufacturers offer kits tailored for hot climates. If not available, consult experts to retrofit your equipment for high-temperature performance.
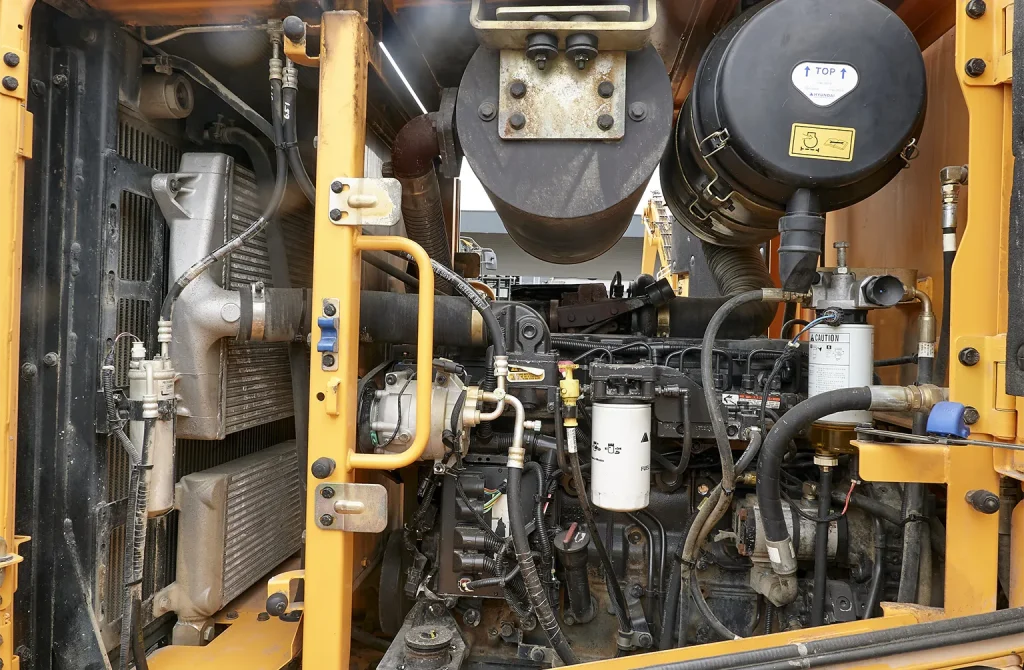
Operator Comfort and Safety: A Crucial Consideration
Humans, like machines, are not immune to the effects of high temperatures. Heat stress can reduce concentration, increase fatigue, and lead to accidents. Here are some tips to protect operators:
- Climate-Controlled Cabins: Equip machinery with air conditioning or ventilation systems to maintain a comfortable cabin temperature.
- Shade and UV Protection: Use sunshades to minimize direct sunlight in the cabin.
- Hydration: Ensure operators have access to cool drinks and encourage regular hydration breaks.
- Work-Rest Cycles: Implement schedules that allow operators to rest during peak heat hours.
By prioritizing operator safety, you not only protect your workforce but also enhance overall productivity and decision-making on the job site.
Conclusion
Operating heavy machinery in high ambient temperatures requires a holistic approach that addresses both technical and human factors. By following these guidelines, you can:
- Prevent costly machine downtime and repairs.
- Protect operators from the adverse effects of heat.
- Maintain efficient and reliable operations even under extreme conditions.
If you are importing used construction machinery, we can help you with the inspection of the existing cooling systems prior to delivery. Mevas inspectors always check the air conditioning, engine cooling and hydraulic system. For more insights and tailored solutions for your construction equipment, contact us today or visit our website.
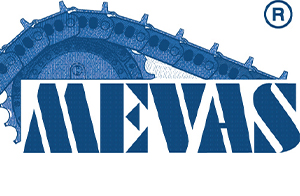
Sponsored by
We are “The Heavy Equipment Inspectors”
MEVAS is your independent service partner for the inspection of construction machinery. Our service is inspection at the highest technical level for all types of larger machinery. Have used heavy equipment inspected by a third party before you buy it. Available in more than 25 countries.